What drives the company Ossiform?
At Ossiform in Denmark it’s all about the construction of patient specific bone implants via 3D print.
Starting as a student project, it has always been the vision to help patients in need by delivering high quality medical devices in form of their P3D Bone solution – Patient-matched resorbable bone implants that facilitate the natural forming of new bone to reconstruct bone deficiencies in patients.
The P3D Bone is purely bioceramic based and printed with a unique bone-like porosity that allows for an effective remodeling into native bone. The result is a more natural implant in terms of material, shape, and structure. With P3D Bone, surgeons will be able to provide an implant that precisely matches patient needs, and thereby improve patient outcomes, increase procedural efficiency, and minimize the risk of complications.
3D printing and 3D scanning go hand in hand
The process of 3D printing is strongly linked to quality control to ensure that the printed products meet match the devised design. For their bone implants, Ossiform follows a couple of crucial steps to meet the pre-determined implant design specifications for a successful patient-matched bone reconstruction. Involved in the process are several iteration loops and the GOM Scan 1 for quality assurance.
1. CT data of damaged body part
The process starts when a patient has a damaged body part which requires reconstruction using bone implants. The bone defects get detected via CT data and forms the base of the work at Ossiform.
2. Implant design
After receiving the CT data, Ossiform starts to design an implant which meets the individual demands of the patient’s bone defect. The implant gets inspected through multiple steps to ensure that it meets all set requirements to be implanted into the patient’s body, in collaboration with the surgeon performing the procedure.
3. 3D printing implants
After finalizing the design process, the 3D printing process of the medical device comes to life in a clean room.
4. Multiple quality control iterations
Maintaining a product which is within tolerance during the complete 3D printing process is a must to ensure exact fit to the patient’s bone defect. Quality control therefore has to be executed before and after post processing the bone implant, to constantly check the specifications of the product. GOM Scan 1 helps here to keep quality high while reducing lead times for the medical devices.
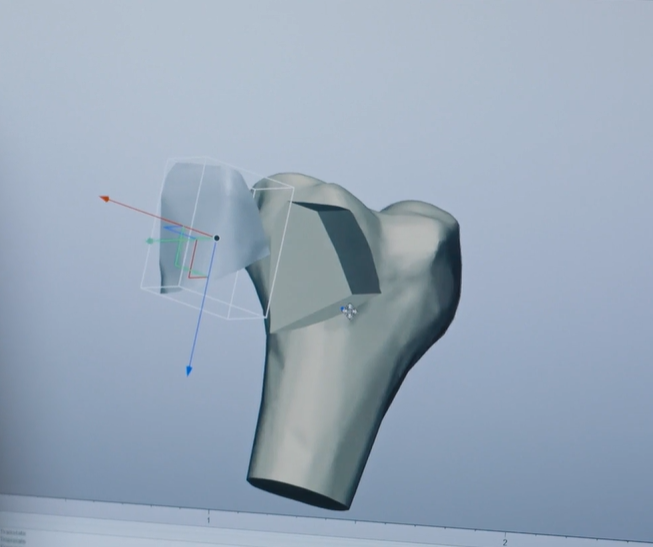
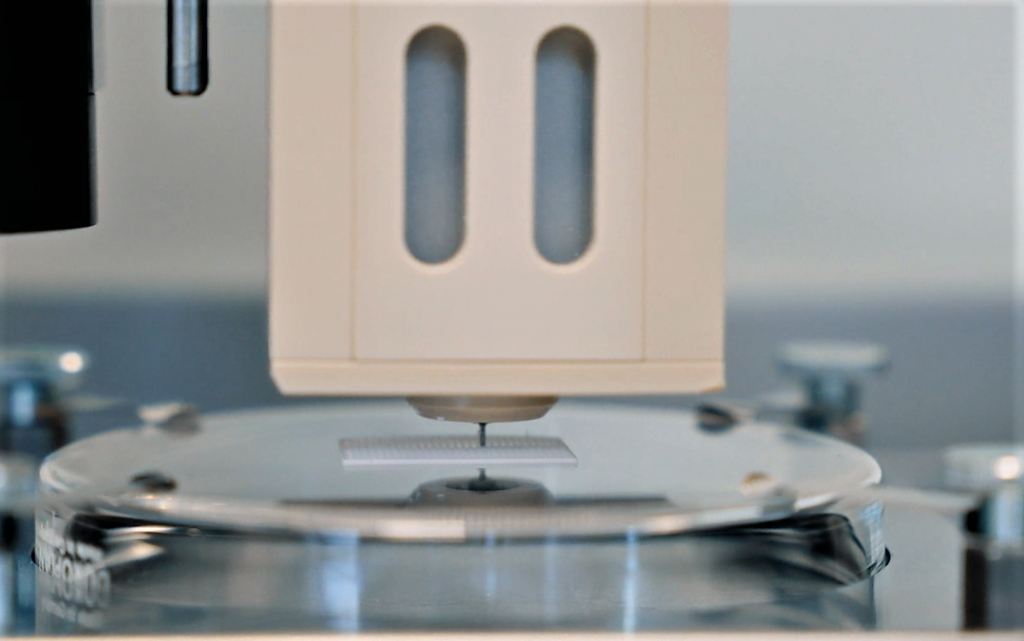

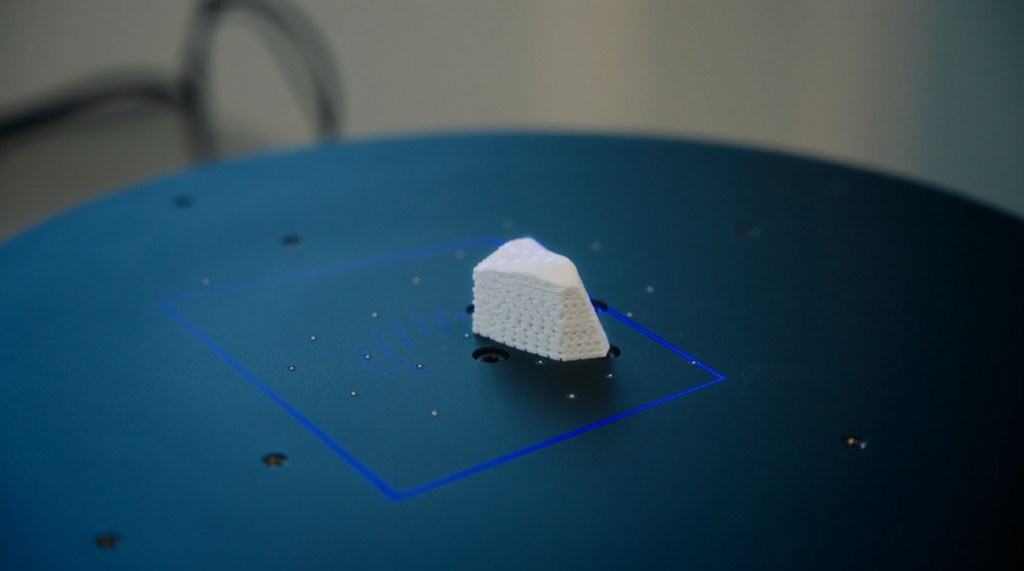
GOM Scan 1 for complex and versatile tasks
Ossiform’s decision to work with GOM Scan 1 came as a result of dialogues with our Danish partner Zebicon who advised and supported Ossiform in the selection and implementation of the system. This resulted in a fast and easy product validation at the company. The 3D scanner allows the company to scan even complex structures of variating implants. The main task here is to check that the dimensions are right through two steps.
1. Quality control of 3D printed part
After printing the initial bone implant, GOM Scan 1 is used to check the quality of the 3D print. Pre-defined tolerances are checked before working further on the object.
2. Quality control of final P3D Bone device
After sintering the implant, a check of the final specification compatibility must be performed. This ensures the customized fit to the patient before being implanted.
The optical solution of GOM Scan 1 proves highly useful because it allows time saving in the quality control. Its easy set-up makes the check of dimensions intuitive and efficient. The compact design of the system is furthermore the perfect fit for the requirements of a cleanroom where space can be limited. Moreover, the data collected is of the highest quality and thus makes even the smallest deviations, which have to be detected before the implant leaves the production, visible.
Evaluating data for exact custom-fit
Due to the multi-step production process of medical devices, deviations from the planned design is possible. With data tailored to the highly individual implants, crucial information on the part quality can be determined. In the ZEISS Quality Suite, divergences are made visible in no time to make sure that produced medical devices are within specification. Another benefit of the inspection software: The measurement results can be exported as a PDF report and stored in the Quality Management System. This way, the final implant gets inspected through multiple perspectives to ensure that it matches the planned design and fits perfectly into the patient’s bone defect.
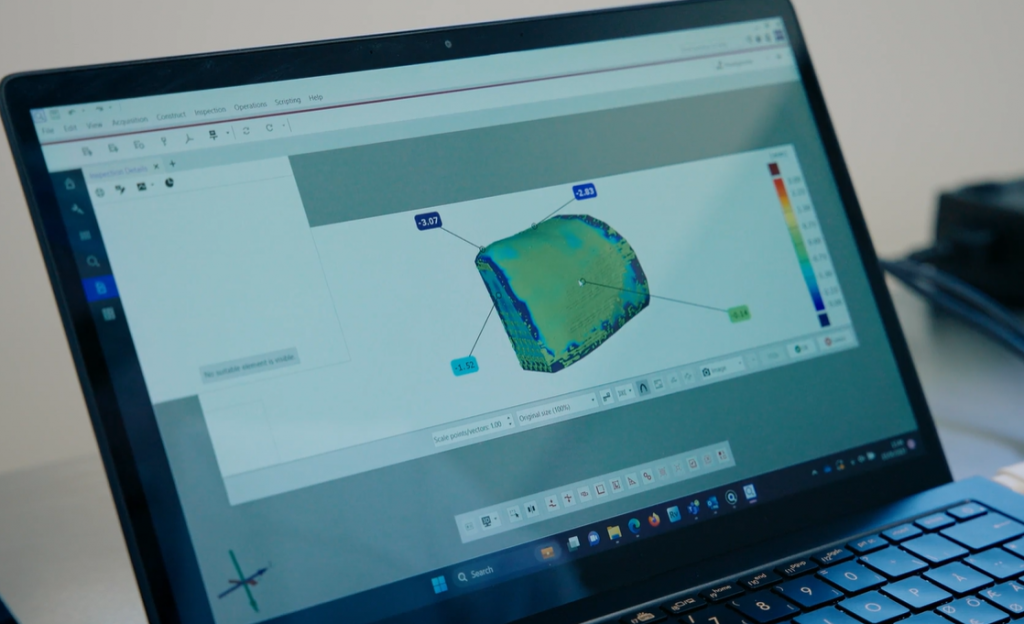
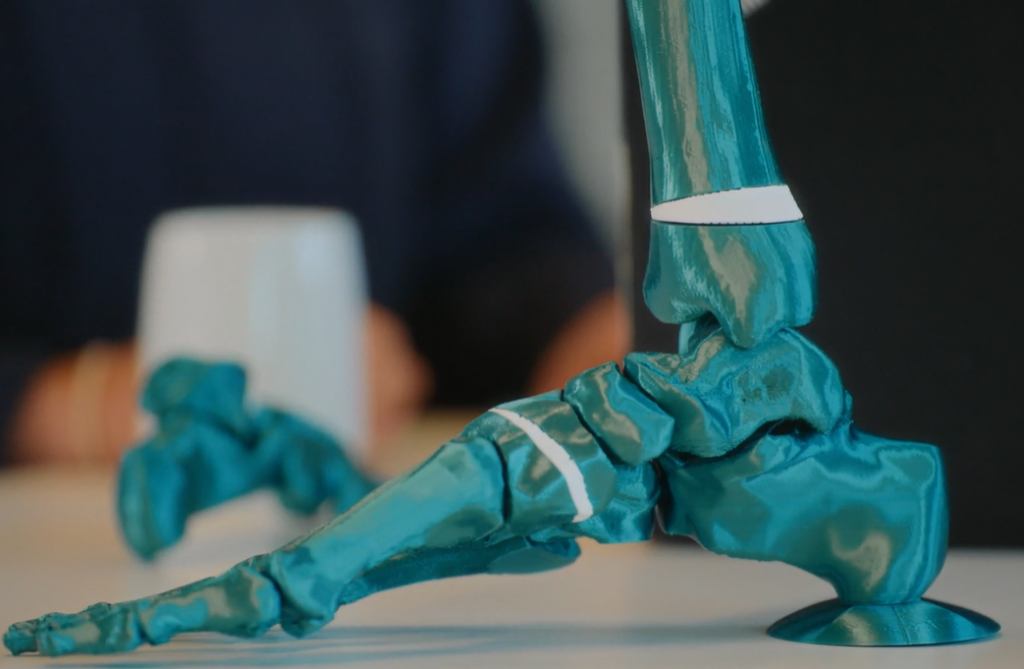
Follow the work at Ossiform
You want to know more about the ideas of the company and its way of quality control for medical devices? Watch our latest Maker Story here: