Große Werkzeuge oder Matrizen für die Blechbearbeitung werden meist aus gegossenen Rohlingen herausgefräst. Zur Herstellung dieser Rohlinge werden Modelle aus leicht zu verarbeitenden Materialien (Styropor o.ä.) gebaut. Dann werden gießereirelevante Zusätze wie Ein- und Auslässe hinzugefügt. Anschließend wird die Form in Gießsand eingebettet. Nach dem Hinterlegen der Form wird das Modellmaterial ausgebrannt und der Guss hergestellt. Der Rohling muss einen Materialüberschuss aufweisen, um Abweichungen beim Einbetten und Gießen auszugleichen. Außerdem muss der Rohling in den aktiven Bereichen einen Überschuss an Material aufweisen, um eine maschinelle Bearbeitung und eine manuelle Abstimmung des Werkzeugs zu ermöglichen. Damit wird die gewünschte Form und Oberflächenqualität des Teils im Stanzprozess erreicht (Abb. 1).
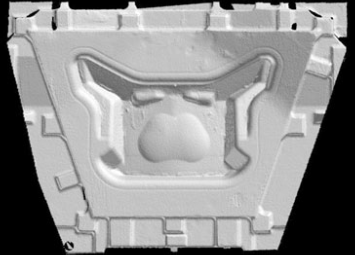
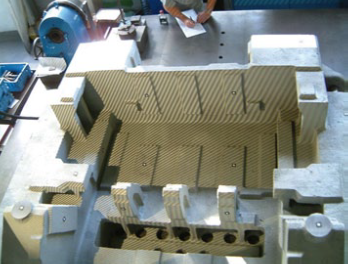
Für die Bearbeitung wird der Rohling auf dem Arbeitstisch einer entsprechend großen Horizontalfräsmaschine ausgerichtet und festgeschraubt. Zunächst wird in der Regel die Unterseite zu einer ebenen Fläche bearbeitet, dann wird der Rohling gedreht und die grobe Kontur des Werkzeugs wird sichtbar. Da die Bearbeitungszeit des Rohlings auf der Fräsmaschine ein großer Kostenfaktor ist, ist eine Zeitersparnis sehr willkommen. Daher werden große Rohlinge häufig geprüft und vor dem Aufsetzen auf die Fräsmaschine manuell mit Ausrichtungsmarken versehen. Anhand der Markierungen wird der Rohling auf dem Frästisch positioniert, ausgerichtet und verschraubt. Mit Hilfe der Pro-Line-Funktion des ATOS Q „Rückprojektion“ können diese Markierungen live auf das Teil projiziert werden. Anschließend werden in der Regel gießspezifische Modifikationen durch Abschneiden oder Abfräsen in manueller Steuerung entfernt. Dann wird der erste Kontaktpunkt des Fräsers mit dem Rohling definiert, indem man den Fräser in der Luft arbeiten lässt und vorsichtig manuell an den Rohling heranführt. Von diesem Startpunkt aus wird mit dem Schruppen begonnen. Da die Schnitttiefe nicht gleichmäßig ist und von der CAM-Software nicht vorhergesagt werden kann, muss eine langsame Vorschubgeschwindigkeit verwendet werden, die manuell überwacht und korrigiert werden.
Auf der Grundlage von Messungen mit manuellen Messschiebern ist eine sichere oder optimierte Ausrichtung eines großen und komplizierten Rohlings nicht möglich. Eine schlechte Ausrichtung kann sogar ein Auftragsschweißen erfordern, um alle relevanten Flächen des zukünftigen Werkzeugs bearbeiten zu können. Für die Digitalisierung von Rohlingen hat ZEISS den ATOS um einen großen Messbereich erweitert. Für die Digitalisierung der großen Gussrohlinge werden Markierungen auf dem Rohling angebracht. Dann wird eine zentrale Ansicht aufgenommen. Anschließend werden weitere Ansichten erfasst und automatisch in die vorhandenen Scandaten übertragen. Mit dieser Technik können Rohlinge mit einer Größe von bis zu 5 x 3 Metern in einer Stunde digitalisiert werden, wobei die geforderte Genauigkeit eingehalten wird. Die Exportdaten aus dem ATOS-System sind entweder eine Datei im „stl“-Format oder Schnittdaten. Mit Hilfe der ZEISS Reverse Engineering Software können wir auch eine CAD-Datei erstellen. Die ATOS-Exportdaten können direkt in CAM-Systeme wie TEBIS (Modul „SCAN“) oder WorkNC (Modul „NCSpeed“ von Sescoi Inc) importiert werden. Basierend auf den aktuellen Daten kann nun die Form des Rohlings in die benötigte Werkzeuggeometrie eingepasst werden. Dann kann eine optimale Passung mit minimierter Bearbeitungszeit definiert werden.
Darüber hinaus kann eine optimierte und kollisionsfreie Schneidbahn mit idealen Schneidparametern und minimierter Schneidzeit berechnet werden, um das Werkzeug in einem vorhersehbaren, schnellen, sicheren und unbemannten Vorgang aus dem Rohling zu erzeugen. Eingesetzt wird das oben beschriebene Verfahren bei BMW, Mercedes und Audi in Deutschland in Zusammenarbeit mit TEBIS und SESCOI. Im konkreten Fall konnte die Zeit auf der Fräsmaschine von 48 Stunden auf 8 Stunden reduziert werden. Wichtig für den Kunden war, neben der Zeit- und Kostenersparnis, der zuverlässige, sichere und vorhersehbare Prozess.
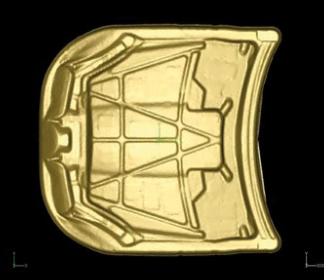
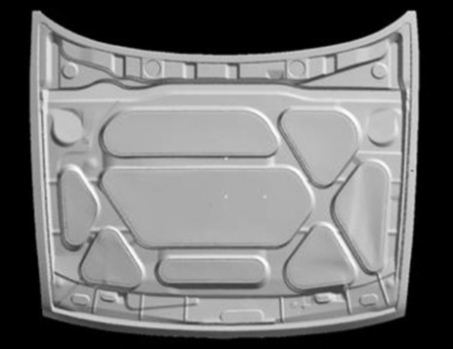
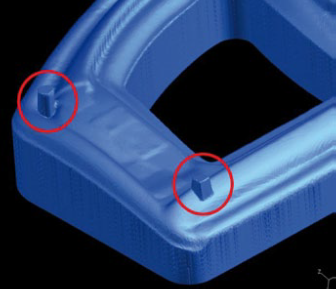
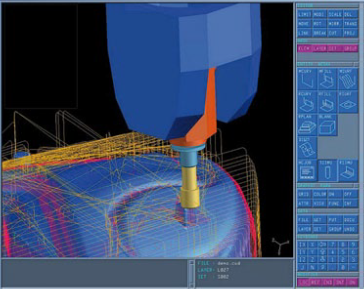
Automobilkunden fragen bei ihren Lieferanten nach einsatzbereiten Werkzeugen mit einer digitalen Beschreibung der tatsächlichen Werkzeugform. Auf Basis dieser Daten kann ein Qualitätskontroll- und Rückverfolgbarkeitsprozess gestartet werden. Der Verschleiß kann quantifiziert werden, eine Nacharbeit des Werkzeugs kann bestellt und mit einer genau definierten Masterform getestet werden. Bei Bedarf kann auch schnell eine genaue Kopie des Werkzeugs erstellt werden. Der Scanner kann darüber hinaus zum Scannen des Werkzeugs für diese Anwendung verwendet werden. Um die erforderliche hohe Genauigkeit zu erreichen, ist ATOS so kalibriert, dass ein kleinerer Messbereich digitalisiert werden kann. Auf dem Werkzeug werden Markierungen angebracht und die genaue Position dieser Markierungen mit Hilfe der Photogrammetrie bestimmt. Dann wird der Sensor eingesetzt, um das Werkzeug zu scannen und die digitalisierten Daten in das durch die Markierungen definierte Raster einzufügen. Durch den Einsatz der ATOS-Technologie kann eine Genauigkeit der gescannten Daten von wenigen hundertstel Millimetern garantiert werden.
Der ATOS-Sensor ist der Standard für die Digitalisierung im Design, in der Produktentwicklung und in der Qualitätskontrolle. Die beiden in den ATOS-Scannern eingesetzten Kameras verifizieren bei jeder Messung die Kalibrierung des Scanners und sind somit eine Notwendigkeit für den Einsatz eines transportablen Systems in der Qualitätskontrolle. Auch der Wechsel des Messbereichs mit Kalibrierung anhand eines zertifizierten Artefakts ist vom Anwender in wenigen Minuten erledigt. Durch diese Möglichkeiten kann das ATOS an unterschiedliche Kundenbedürfnisse angepasst werden und liefert genaue und effiziente Ergebnisse.
Lerne das System kennen!
Du möchtest mehr über unsere 3D-Scanlösungen erfahren? Besuche unsere Website oder kontaktiere uns für eine kostenlose Demo.